A day in the life of an Estate Manager: Pool Project
- Handgraaf Estates
- Oct 5, 2021
- 3 min read
Updated: Oct 6, 2021
Property Managed by: Handgraaf Estates
Contractor: S.C.S. Concrete
One of the bigger projects on our to-do list this year was the Pool Remodel.
The 100,000 gallons (Olympic size) pool itself was 15 years old and had a few unique features. Namely, the deep end of the pool was deep enough to meet the requirements (11.5 ft.) by CA. law to have a diving board installed.
Secondly, because the principals are avid swimmers, they designed the pool according to an ''overflow'' system. Which means that the entire pool was surrounded by round edges where the water would flow over. The benefit of this type of design is that it leads to less resistance when swimming, as the waves won't bounce back from the walls (they roll over into the gutter and filter).
Thirdly, all the pool equipment was located 12 feet underground and could only be accessed by opening a hatch and climbing down the ladder.
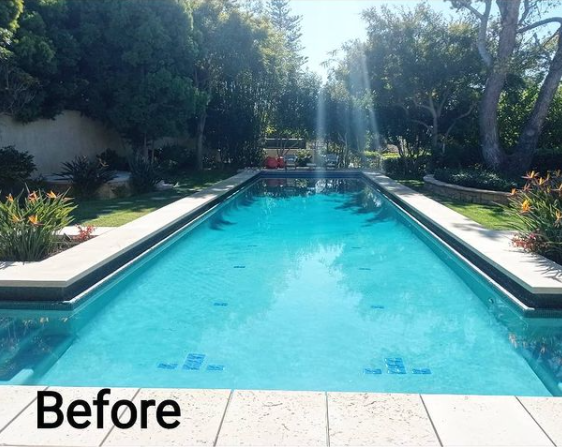

As can be seen above, over time, the overflow design does come with its shortcomings. Because the warm pool water flows over the round edge, it heats the material followed by the air then cooling it. This constant temperature change of hot / cold leads to contraction and expanding of the material, which over time leads to the tiles peeling off.
Solely repairing the tile line wasn't an option either. As in order to get to the tiles, the water level had to be lowered. Which then would expose the plaster which would discolor it to a complete grey mess. Meaning that the only viable option would be complete remodel.
Initial phase
Because we work with a preferred vendor list (and black list for that matter), we invited our chosen contractors to the property to evaluate the project.
After all the bids were in, we presented everything to the client including the samples of the new material. The choice landed on S.C.S. Concrete due to their professionalism, really getting into the details on what the best way would be to go about the project and them being the one stop shop for nearly all the work.
The initial 20% was paid and the project could officially start!

Demolition
A date had been set and the emptying of the pool began. It look 2 pumps a total of 4 days of around the clock pumping to get the pool completely empty.
As soon as the shallow end was dry, the demolition of the tile water line could begin. As you can see below, the heavy stone covers were removed, as well as the diving board, and the pool cover was unscrewed and rolled back to allow for more work space.
All this was done by S.C.S. Concrete, other contractors stated that the principal would bare the responsibility of removing the heavy stone covers, the diving board and unscrewing and removing the pool covers, S.C.S. Concrete came through and did an outstanding job without damaging any of the material.


Tile water line
After a dusty 10 days of jackhammering, the demolition was complete. It now was time for the new tiles to be installed.
Because of the overflow design of the pool, it was absolutely crucial for all tiles to be exactly level and fit perfectly. With the new tiles coming in square sheets, they needed to be placed into position by hand. A very intricate job that was conducted and performed with perfection.
After the completion of the tile water line, removal of debris and a thorough clean up, it was time for the plaster.

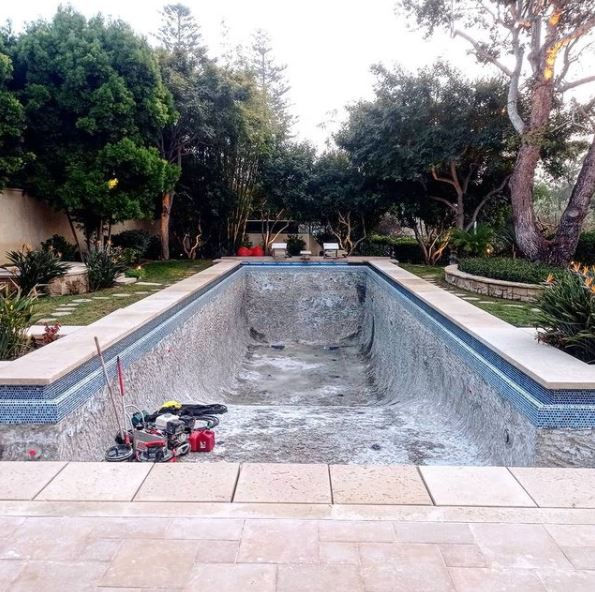
Plaster
Due to the sheer size of the pool, it took 16 people to mix, apply and smoothen out the plaster.
An important detail to note here was that these 16 people all brought their own vehicles with them. S.C.S. concrete ensured that every single car on the property had a flattened carton box underneath the engine when parked, catching any oil or other leaking liquids that would otherwise stain the driveway.
Once the all the plaster was applied, it look 2 hoses ''only'' 2 days to fill the entire pool and harden the plaster.

Completion
The end result was better than we hoped! Because we picked the white grout lines (on recommendation of S.C.S. Concrete), the pool now looks better than it ever did before.
Needless to say, the principal was very happy to say the least and we will surely be contracting S.C.S. Concrete for our future projects!

For the full video of the property and end-result of the pool:
Property Managed by: Handgraaf Estates - www.HandgraafEstates.com
Contractor: S.C.S. Concrete - www.scsconcretedecorations.com
Comments